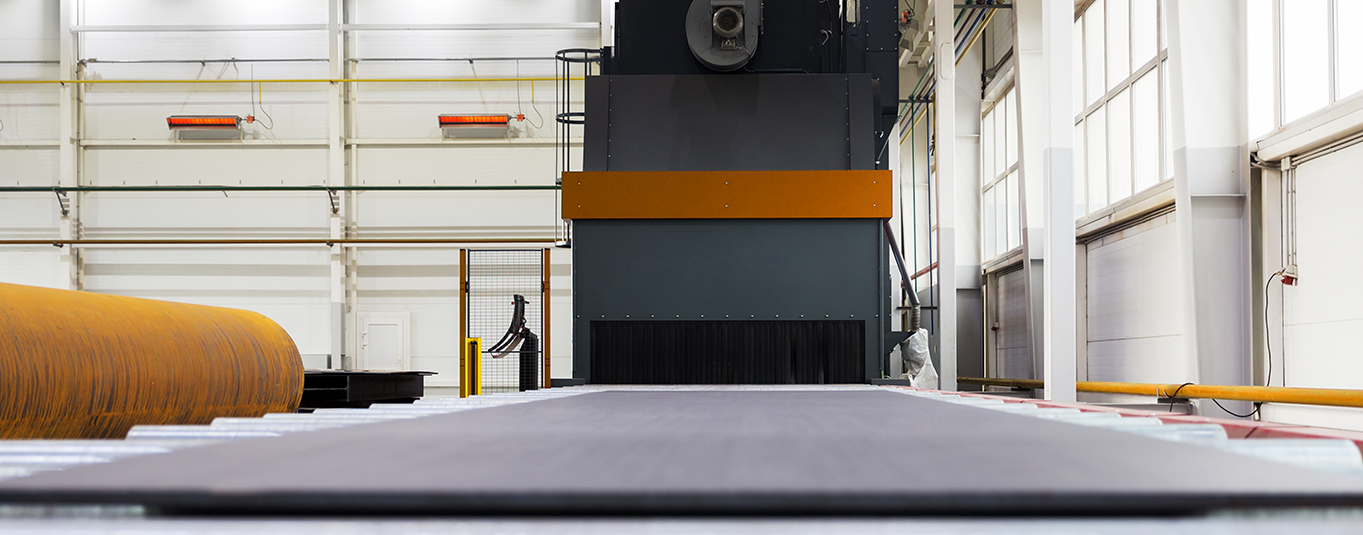
Airless shot blasting equipment also known as peening or wheel blasting creates a stronger, polished metal when done properly and is commonly used in the aerospace, automotive, construction, shipbuilding, rail and foundry industries to mention a few.
From pre-fabricated machines to custom applications for your airless wheel blasting process, BlastOne can consult or advise on which application may be most suitable for your peening needs. We carry monorail, roller conveyor, spinner, hanger, table, tumblast and full blast and paint line systems.
With properly setup equipment, your airless wheel blaster will be the optimal method of cleaning and preparing your surfaces for paint.
BlastOne carries all the parts, accessories, and media needed to keep your wheel blasting and shot peening equipment running. We also provide rental equipment, consulting, and custom engineering.
HOW WHEEL BLASTING WORKS
Wheel blasting or peening equipment, directly converts electric motor energy into kinetic abrasive energy by rotating a turbine wheel. With these large amounts of accelerated abrasive, wheel blast machines are used where big parts or large areas of parts have to be de-rusted, descaled, de-burred, de-sanded or cleaned in some form prior to coating.
Often the method of transporting the component parts to the blast machine will define the type of unit to be installed. Simple table machines allow for easy manual hand loading of small components. Integrated automatic roller machines may require pullies and other lifting equipment to position components. While on the largest end of the scale there are complete crane roller conveyors and track systems.
DIFFERENCES BETWEEN WHEEL BLASTING / PEENING AND ABRASIVE AIR BLASTING EQUIPMENT
The key difference between using the methods of surface preparation is the process used during the blasting. Shot blasting is the process of using a throwing wheel to propel the abrasive media at the surface of the object to be prepared. While the abrasive air blasting process incorporates the use of compressed air to create a stream of abrasive that is directed towards the objects surface.
During shot blasting, abrasive gets acceleration through the throwing wheel, which is rapidly turning in a special steel housing, with one side oriented opening. Shot blasting is used for blasting metal, different profiles and welded constructions. The process is controlled within the production machine and require far less manual labor during the blasting process.
Animated Wheel Machine Overview
Extensive Wheel Machine Range
Able to accommodate areas and items of any size in many different systems.
Monorail Blast Machines
Used with an overhead monorail conveyor, these wheel machines can be designed for higher throughput than the Spinner Hanger. Typically powered by a chain conveyor or self-powered drives, the parts on hangers are automatically cleaned and transferred to the unload station.
Roller Conveyor Systems
Fully automated wheel blast systems designed to descale and remove rust from plate and structural members prior to fabrication. Specially developed to meet the needs of the fabrication industry. Effectively cleans large work pieces, eliminating the environmental problems and high labor costs associated with manual air blasting.Unit typically has 4 wheels.
Spinner Hanger Systems
Designed to blast clean work pieces on an overhead conveyor, the Spinner Hanger wheel machine rotates the work hanger to achieve maximum exposure of the parts to the blast streams. Various designs including turnstiles, Y-tracks, and flow-through cabinets are available to suit a range of requirements. Used to clean casting and large parts that cannot be tumbled. Unit typically has 2-4 wheels.
Table Machines
Rotary table wheel machines include both door mounted swing tables and cabinet mounted tables. Clean castings and large work pieces that may not be suitable for a Tumblast or Spinner Hanger. Designed for rugged operation, rotary tables are among our most versatile machines.Unit typically has 1-2 wheels.
Tumblast Systems
Tumblast wheel machines offer excellent reliability and versatility for high performance batch cleaning. Designed to suit a broad range of requirements and operating conditions. Machines equipped with rubber work conveyors provide less aggressive tumbling of fragile work pieces. Can operate on a continuous, unmanned operation with the effectiveness of batch cleaning.
Unit typically has a single wheel.
Blast and Paint Lines
Prior to cutting, steel plates are blasted to remove millscale before a primer coating is applied. The system incorporates a preheating furnace, a pass through shot blast unit, automatic paint booth and a slat conveyor carrying wet products through the drying tunnel. Various plate & profile widths are automatically identified & coated with the weldable primer in a continuous process.Unit typically has 2-8 wheels.