INTRODUCTION
Due to government legislation and general community environmental concerns, the pressure is upon many work yards and production sites to reduce waste and therefore manage landfill options most effectively.
Notably in every 1000sqm of site project coated surface, there is generally a mass of waste that requires management – up to 40 tons.
In “shop” situations we know that the abrasive can be recycled – however the remnant dust and particulate matter still requires management of recovery, and disposal. Solvents can be recycled – and disposal of the remnant solids is a costly affair – up to $6000 per quarter.
In “site” situations we also know that our generation of waste material can be affected by other environmental & site factors – such as rainfall, hazardous coating removal, various carcinogens and even mercury, molybdenum, arsenic and asbestos. Solvents are usually recycled day-to-day, then the dregs are returned to the waste bin?
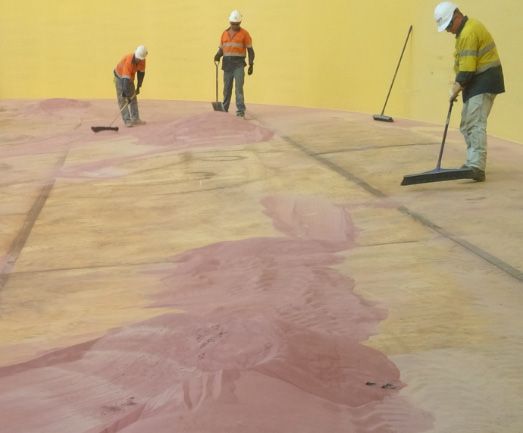
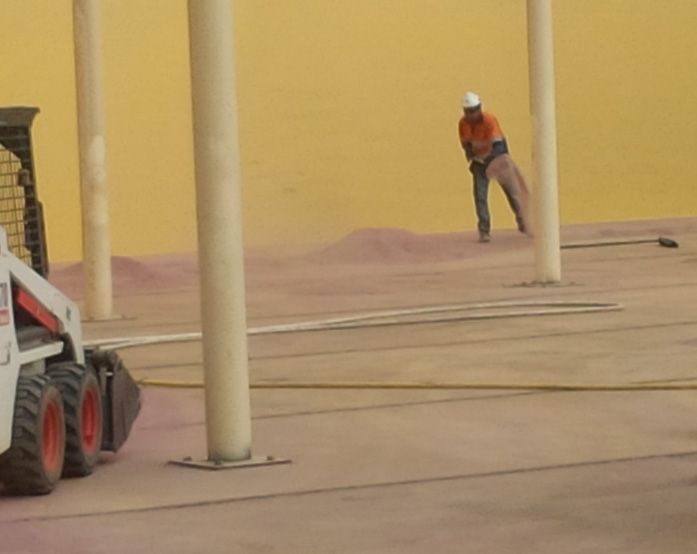
Paint and solvent recycling units use simple distillation. Excess paint is poured into the machine’s plastic liner and the lid is closed. The paint is heated until the solvent boils into a vapor and the paint residue is collected as a powder. The vapor is then cooled and the solvent drips into a collection tank to be reused. The paint solids retrieved during the recycling process can be reformulated into quality paint coatings.
These substances mix only sparingly with water. As they are slowly broken down in water, they deprive aquatic organisms of the oxygen they need to survive. The toxic nature of chemicals in solvent-based paints may also cause tumors to form in animals such as fish. These paints can contain heavy metals such as lead, chromium, mercury and zinc. Heavy metals accumulate in the environment and can lead to long-term problems like sediment contamination and poisoning throughout the food chain. This can eventually affect humans.
Section 16 of the Waters Act 1992 prohibits people from polluting waters. Disposing of wastes from painting into waters constitutes pollution. Under Section 16 of the Act; any person or body corporate may be guilty of an offence, and liable to punitive action under the Environmental Offences and Penalties Act 1996. These penalties can involve a fine of up to $1000. More serious breaches of the Waters Act can attract a penalty of up to $1,250,000 for a corporation, or up to $250,000
SOLVENT BASED PAINTS
Solvent-based paints (alkyd or oil-based) require special disposal practices. Solvent-based paints are ignitable and present particular hazards. They should be disposed of as a hazardous waste.
Generally the agreed practice is to collect and store such wastes until there is sufficient quantity to be collected by an approved waste contractor. Speak to your waste contractors (numbers in the Yellow Pages) as to what quantities are economically viable to be collected for your location.
These substances will generally be transported where facilities exist for the destruction of these hazardous wastes.
The easiest way to manage waste is to bundle it up and pay the top price for management of same at a waste station. The problem here is that the “top price” can adversely affected your profitability – and possibly risk your future business viability.
Some waste transfer stations can charge up to $2000 per ton to manage receipt of your waste.
ABRASIVE ANALYSIS
The choice of your site clean up METHOD can have a surprising impact on the cost of a project.
What the leading companies are doing is looking at the cost of the project.
The cost of cleaning up spent abrasive can double – if you choose upon price rather than efficiency!
When you look at your project P&L, what is the biggest line item? Generally labor right?
Then why spend twice the labor hours cleaning up double the amount of abrasive, when other contractors use ½ the amount?
WHAT COST WOULD YOU LIKE TO AFFECT THE MOST?
However, the financial aspect isn’t the only consideration when deciding on abrasive and coating, there is actually 3 key decision points to make when choosing abrasive:
Project Cost
What abrasive & coating will result in this project being completed most cost effectively?Regulations & Health Effects
It’s only prudent to consider the health & environmental impacts of the different abrasives, coatings and solvents.Specifications
What abrasive & coating will produce the desired finish within specification?
We will cover all 3 points in detail, however lets first do a basic overview of all the common facts in a coating project of industrial structures.
PROJECT COST
The single biggest key driver of project cost is the timeline of the project. As per the above diagram, labor usually accounts for around 60% of a project cost, and is the biggest area where cost can blow out or be saved. Different abrasives & coatings can perform differently and contribute to excessive labor, waste volume and disposal costs.
We can evaluate these costs in the following 3 areas:
Daily completed coated area
Daily consumption of abrasive, coating and solvent
Disposal cost of waste abrasive, containment, paint overs and materials
The true cost of a finished coating is the actual cost per square meter on the surface.
There is a simple formula that can be used to determine the cost per sqm meter that takes into account abrasive, labor, equipment, clean up disposal, and production rates.
Abrasives | Garnet | Platinum Grit |
Disposal | 11,419 | 48,600 |
Equipment | 17,500 | 75,000 |
Labor | 1,967 | 4,400 |
Abrasives | 18,000 | 52,000 |
Total | 48,885 | 180,000 |
SpeedBlast Savings = 73%
THE COST OF CHOICE
Different abrasives dig deeper into the steel, creating deeper surface profile.
This consequently means that you’ll use MORE PAINT to cover the deeper profile, than maybe you allowed for!
TWICE THE COATING USAGE
Excessive surface profile depth created the need to ‘fill’ the profile to enable the required Wet Film Thickness. You need TWICE the paint to cover the DEEP profile.
TRANSER EFFICIENCY
Transfer efficiency is the amount of paint solids deposited on a part divided by the total paint sprayed and is expressed as a percentage of solids/weight.
Transfer efficiency means the amount of paint that leaves from a spray gun and coats the intended product
Overspray is wasted paint that does not end up coating the product
Transfer efficiency ranges greatly form 20% up to as high as 90% with the best conditions and equipment
The benefit of high transfer efficiency is that it will save you on paint cost
Application method and transfer efficiency
REGULATIONS AND HEALTH EFFECTS
Health factors are another factor to take into consideration.
Crystalline silica is recognized world-wide as a Class 1 Carcinogen.
The heavy metals and contaminants recovered in the waste clean up process, can cause additional risk and elevated fees!
When blasted against a surface at 750 kms per hour, some abrasives are pulverized into extremely fine dust, and some slag abrasives release heavy metals.
Many countries have regulations around this, of note is the current US Beryllium rule.
WHAT ARE YOU REALLY PAYING FOR?
85% PLATINUM GRIT
CaO (Calcium Carb) 5-10%
Cr203 (Chromium) 1-5%
86% INDIAN BEACH/RIVER GARNET
SiO2 (Quartz) 9%
FeTio3 (Ilmenite) 5%
100% GMA ALLUVIAL GARNET
100% usable abrasive
SUMMARY
When choosing the abrasive, coating type and solvents for your project, it is important to consider all the costs associated with the recovery of used materials, and management of waste and disposal.
-
Project Cost
- What abrasive type & coating will result in this project being completed most cost effectively?
-
Health Effects
- It’s only prudent to consider the health & environmental impacts of the different abrasives and solvents?
-
Specifications
- What abrasive will produce the desired surface finish with the correct profile cleanliness, with minimal waste?
CASE STUDIES
Contact BlastOne
We love to talk to customers and help them make the best decisions when purchasing equipment.
You can reach us via our Live Chat, Email, Phone, and Online Form.